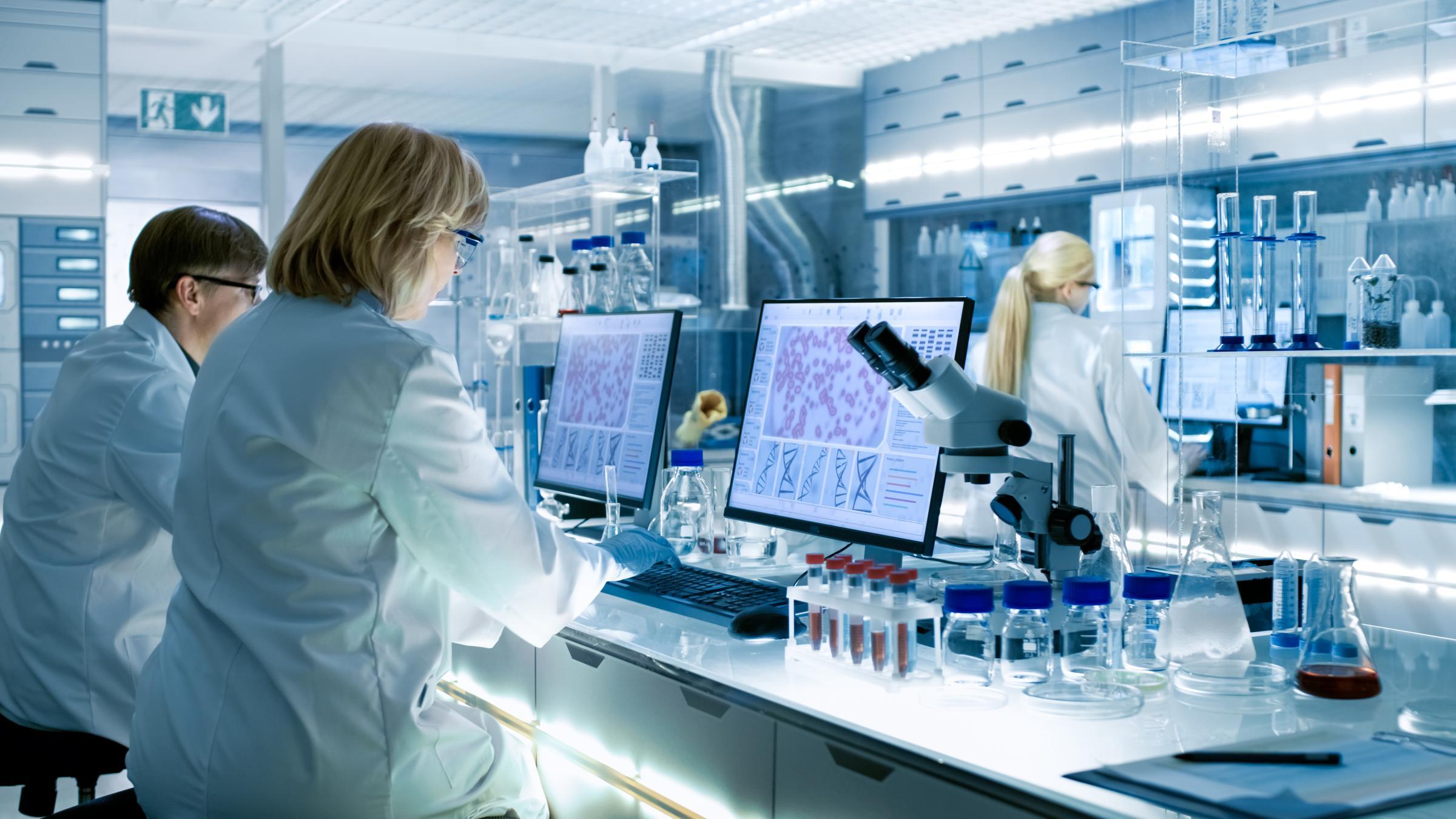
Hygiene Monitoring
Principle Cleaning Services Keeps a Prestigious Research Institute Running During the COVID-19 Pandemic
Principle Cleaning Services is a market leader in providing corporate, commercial cleaning in London. Established in 1989, the company is privately owned, has an annual revenue of over £60 million and employs over 2,200 people. Supporting and delivering clean environments across London, their clients include many of London/s most well-known businesses and their iconic landmark buildings.
Principle Cleaning has developed Safe Space to support their customers in mitigating the risk of workplace infection and to give their teams the confidence to return to work. With a focus on maintaining high levels of surface hygiene, Safe Space sets out 3 stages to deliver confidence and safety to the work environment. Stage 1 involves scientific verification using ATP testing to document current hygiene practices. Stage 2 involves submitting recommendations to improve facility hygiene to ensure building cleanliness. Stage 3 is about consistent and constant review to ensure cleaning remains effective, even as building occupancy increases.
In the wake of the COVID-19 pandemic in 2020, most of Principle Cleaning's work was demobilised due to people working from home and a government-enforced lockdown. However, one of their largest customers, a prestigious research institute, requested 12 additional full-time staff (to complement the existing 33 positions). The reason? The research institute stopped all non-essential science to concentrate its efforts on COVID-19 research and needed to keep its scientists safe while working in close proximity to each other. They also opened a drive-through testing center which allowed key workers to be tested 24/7 and also provide quick turnaround testing for cancer patients from London hospitals that needed life-saving operations.
Principle Cleaning responded quickly and efficiently to this request, providing staff, resources and cleaning services to keep all areas clean and safe within the research buildingas well as in the testing areas. Principle Cleaning staff were trained in Amber Clean (standards by the National Health Services for cleaning - Red/Amber/Green) and used this procedure to clean testing pods throughout the pandemic and continue today.
In addition, whenever a positive case was identified within the facility, the Amber Clean process was followed by Principle Cleaning staff; at peak, 20 hours of Amber Cleaning occurred in a month. To clarify, Amber Clean is an enhanced cleaning process where standard housekeeping cleaning agents are replaced with a chlorine-releasing disinfecting agent and all touchpoints are thoroughly cleaned.
Solutions
Principle implemented the following solutions to keep the research institute up and running:
- Provided additional staff to clean and sanitise touch points for 12 hours daily, keeping scientists and key workers safe (see Figures 1 and 2 for representative data).
- Provided Amber Clean training, (hospital grade sanitation) for site staff. The cleaning process involves operatives to wear full PPE, the usage of disposable materials for each job and the manual wiping and sanitising of all surfaces (vertical and horizontal) within a particular area.
- Established Amber Cleaning services for NHS Swab Test pods and Vaccination Center.
- Provided clear, detailed communication by daily reporting and catch-ups via the account manager, monthly client report meetings with the directors, and quarterly meetings with the head of operations.
As a result, this institute was able to fully support COVID-19 research while ensuring the safety of all in the building. According to the Facilities Manager at the institute, ”We have had volunteers testing COVID swabs, scientists working round the clock, the catering team feeding everyone when all shops closed but I have to say that the cleaning team was invaluable in keeping us clean and safe while we worked. As the virus cases increased, so did our rate of infections in the building, and that's when we needed the cleaning team to spring into action. We also had to repurpose our facilities and Principle were invaluable in helping us achieve this.”
Peter Smith, CEO of Principle Cleaning, also highlighted, “I have always had great admiration and respect for our cleaning staff, when I go on-site during the day, and especially early morning, when I may have struggled to get up to meet a site team, there they all are smiling, well-presented and full of energy. During the pandemic, nothing seemed to change, the world was closed, but when I went to one of our contracts that were operating, there they were, the cleaning team, keeping buildings open, clean, and safe for staff to go about their normal work. We are very lucky to have such a dedicated team of fantastic cleaners.”
Requirements
Principle Cleaning prides itself on innovation and sustainability. As the research institute was responding to the pandemic, they worked in partnership with the Institute to implement initiatives to demonstrate confidence in meeting COVID-19 requirements. These included:
- PCS-Connect - a washroom monitoring system that provided needs-based cleaning by counting the footfall in washrooms and determining the levels for cleaning and sanitisation.
- Hand sanitising dispensers - Over 50 automatic dispensers, alcohol and non-alcohol gel plus surface wipes and moistening creams were distributed throughout the building. This was a specific request of the scientists based on extended glove-wearing in the labs.
- Antimicrobial surface spray - Surfaces were sanitised and fogged with Zoono, an antimicrobial spray, and key touchpoints were fogged at least monthly, providing a long lasting, residual effect.
- Environmental monitoring to verify cleaning was effective - The Hygiena® EnSURE® Touch and UltraSnap™ testing devices were obtained from Gem Scientific Limited, who are experts in the field of ATP hygiene monitoring, to test surfaces for residual organic matter. Based on ATP bioluminescence technology, high values, expressed in relative light units, indicate insufficient cleaning so recleaning must be performed before sanitising.
ATP Testing
Collectively, this full monitoring system was shown to ensure that surfaces were clean. As part of the monitoring system, an intense training program was established. This program, Safe Space, involved reviewing specifications for cleaning and testing, and using ATP testing to verify cleanliness. Part of the process involved pre-cleaning and post-cleaning testing to demonstrate the value cleaning brings, and the extra value that numerical data brought to the process (see Figures 1 and 2 for representative data). It wasn't considered clean unless the data demonstrated it. In fact, testing as part of pre-cleaning showed that only 58% of surfaces passed the “clean” test. Once the cleaning process was fully implemented and all staff were fully trained, the percentage passing improved by over 44%.
Upon reviewing the data, it was clear that specific areas were “hot spots” or areas with high initial ATP RLU values (i.e., failing the cleanliness test). These areas included the canteen microwave, handrails, lift call buttons and the “tea point 2nd” (microwave on 2nd floor). These locations were ideal to demonstrate the effectiveness of the cleaning methods implemented to protect the staff. Results (Table 1: Data) show improvements of up to 97%, represented as a reduction in RLU counts - showing the impact of rigid cleaning processes on surface cleanliness. In a few instances, counts were already low (male changing room, meeting room table 1) but cleaning still reduced those counts significantly.
Contamination Risk
By utilizing the EnSURE® Touch luminometer, the team identified a number of risks for cross-contamination. Eating areas and microwaves appeared to have the highest levels of contamination, resulting in a process change within the research institute. By eliminating this contamination issue with enhanced cleaning methods, a safer work environment was created. The luminometer and test devices were so easy to use, they began showing managers how to test monthly. The testing also allowed the facility to set a baseline/threshold reading for testing. If the RLU value was over 100, cleaning had to be redone.
Summary
Because the research institute has many scientists working to stay safe while researching the virus, it was vital to keep surfaces as clean as possible, generating the lowest RLU values. Principle also demonstrated how the data from the EnSURE® Touch and UltraSnap® devices helped validate that cleaning worked - moving forward, they can show any client proactively how clean a surface really is.